- English
- Español
Estudiantes de la Ulima triunfaron en el concurso de proyectos del INTERCON 2015
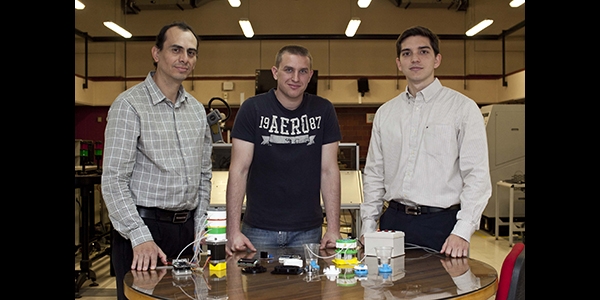
Del 3 al 7 de agosto se llevó a cabo el XXII Congreso Internacional de Ingeniería Eléctrica, Electrónica, Telecomunicaciones y Computación INTERCON 2015 en la ciudad de Huancayo, donde además de las conferencias internacionales, tutoriales y presentación de investigaciones se desarrolló un concurso de proyectos en el que compitieron 11 trabajos de alumnos de diferentes universidades del país. Manuel Vergara y Mauri Gelmi, alumnos de último ciclo de la Carrera de Ingeniería Industrial de la Universidad de Lima, ocuparon el primer lugar con el proyecto “Dosificador de solución de iones ferrato por peristáltica”, trabajo de ingeniería eléctrica que trata sobre el diseño, fabricación y control de una bomba peristáltica, utilizando una impresora 3D para el prototipo y máquinas de corte de control numérico CNC para su manufactura. Ellos diseñaron y fabricaron esta pieza, trabajando junto con los profesores Fabricio Paredes y Víctor Sotelo, para apoyar la investigación de otro docente de la Ulima, Javier Quino, quien busca la purificación de las aguas servidas. El segundo y tercer lugar lo ocuparon proyectos ejecutados por alumnos de la Universidad Nacional de Ingeniería (UNI).
Apoyo para una investigación del IDIC
Acerca de los objetivos de este proyecto vencedor, el docente Fabricio Paredes comentó:
“Lo que queríamos era incorporar la nueva tecnología 3D a los proyectos de los alumnos, así que se pensó fabricar un producto totalmente diferente. Para esto, las bombas nacen como una necesidad de un proyecto de investigación del profesor Javier Quino y eso fue lo que nos impulsó realmente a realizar este proyecto. Se estuvo trabajando en algunas alternativas diferentes y lo que se pensó fue, en realidad, fabricar algo bastante práctico con la menor cantidad posible de piezas, y ahí involucramos la impresión 3D y la electrónica y la programación en lenguajes. Lo que han hecho nuestros alumnos en la práctica es aplicar los conocimientos adquiridos a lo largo de sus estudios y lo hemos plasmado en un producto final”.
Al respecto, Mauri Gelmi complementó:
“Básicamente hemos podido utilizar todo lo que hemos aprendido en varios cursos, como Mecánica, Máquinas o Automatización Industrial, para llegar a un producto hecho con la impresión 3D, hacer piezas en CNC y aplicar los temas de electrónica, que Manuel ha aprendido, para poder lograr un producto que le sirva a otro profesor de un curso de química, que es el profesor Quino, quien hace una investigación aparte para el IDIC. Él nos pidió un equipo para dosificar la solución que quería utilizar para descontaminar el agua servida, esta solución que se va a dosificar retira el cianuro del agua y el profesor necesitaba un equipo para poder dosificar esta solución en cantidades precisas. Quedamos en una bomba peristáltica porque justamente la bomba se caracteriza por ser precisa y no tener contacto con la solución por dosificar, así que era la indicada”.
Todo está en 3D
Manuel Vergara habló acerca de los procedimientos empleados para confeccionar la pieza:
“Utilizamos la impresión 3D porque era lo más rápido en el momento para hacer un prototipo. La ventaja es que es muy sencillo crear piezas con el filamento, y si salen mal se pueden modificar muy fácilmente. Es bastante prueba y error. Como no era tan precisa la impresora 3D, se hicieron varios modelos y se fueron ajustando los tamaños hasta que quedara un prototipo bastante eficiente”.
Mauri Gelmi, por su parte, dijo:
“Esta es la ventaja que otorga la impresión 3D, hacerlo a un menor costo que fabricar un prototipo de metal en CNC. Primero hacer el prototipo con el plástico, el PLA o el ABS, que son relativamente baratos en comparación con el acero, y después ya al finalizar el prototipo puedes trabajarlo en metal. Nosotros nos dimos con la sorpresa de que el prototipo de impresión 3D igual funciona con los esfuerzos generados por el trabajo, y se podría utilizar la bomba impresa con material de PLA o ABS”.
Necesidad de competir
Respecto de lo que los impulsó a presentar su proyecto al INTERCON 2015, el docente Fabricio Paredes fue claro al asegurar:
“Como meta, junto con el profesor Sotelo, que es parte del equipo, lo que siempre pretendemos es concursar, salir de la Universidad para poder ver otros proyectos y también aprender. En este caso nosotros, a finales de febrero, con el profesor Sotelo habíamos tenido algunos proyectos y apostamos por este, así que lo inscribimos y comenzamos a trabajar en él. Ya casi al finalizar marzo los documentos estaban hechos y el prototipo en un estado bastante avanzado, así que empezamos a perfilarlo y depurarlo hasta llegar a lo obtenido. Después de haber conseguido este producto, otro investigador, que es el profesor Morales, nos pide realizar otro tipo de bomba bajo el mismo concepto, otro modelo con cuatro rotores y que es básicamente una bomba en paralelo; es una extensión del primer proyecto, se presenta como una alternativa en el 'paper', pero cuando nosotros concursamos ya teníamos el producto terminado. Presentamos ambas propuestas”.
Cuando les consultamos acerca de la reacción de quienes calificaron la propuesta, Mauri Gelmi recordó que
“las preguntas fueron todas respondidas, eran sobre la bomba peristáltica y un poco sobre la electrónica. Una de las dudas fue si era escalable y efectivamente lo es, pero al ser bajas las concentraciones se tienen que dosificar, aunque aún así esta bomba se puede utilizar. El hecho de que haya sido realizada con impresión 3D significa que en caso se rompa algo, o necesites crecer en tamaño, fácilmente puedes ir, aumentar el diseño en la computadora e imprimirlo; el proceso es bastante simple, lo que toma tiempo es la impresión en sí”.
Con aplicación práctica
Acerca de los usos que se le pueden dar a la pieza preparada por los estudiantes, Manuel afirmó:
“Las bombas peristálticas se utilizan mucho en la diálisis y cuando tienes líquidos que no pueden estar en contacto con las piezas en sí. En este caso tienes la ventaja de que el líquido solamente está en contacto con el tubo y con la manguera, entonces es mucho más higiénico en ese sentido, y también lo único que tendrías que cambiar es la manguera, por lo que los costos de mantenimiento serían muy baratos”.
Mauri, por su parte, insistió en que este producto,
“a fin de cuentas, es parte del proyecto del profesor Quino, y la idea es que mantengamos el proyecto en pie, asistiendo al profesor en caso tenga alguna mejora que hacer, si es necesario hacer un producto terminado con otro material o si cambia su proyecto, porque es parte de una patente. Si él necesita hacer algo específico con la pieza, en realidad se puede cambiar en el momento. La idea es que sea empleado por el profesor y él ya nos dijo que funcionaba y no hay ningún inconveniente con la bomba. Es una pieza para su proyecto, dentro de todo el sistema global. El objetivo del proyecto del profesor Quino es la purificación de las aguas servidas, en este caso la solución de ion de ferrato retira el cianuro del agua y este equipo se encarga de dosificarlo, en la medida en que sea necesario, según el sensor de óxido-reducción que está dentro del agua, que comanda el controlador y el controlador comanda el caudal de la bomba, o sea las rpm del motor”.
Mira el video sobre el proyecto ganador aquí.